Case studies
- DHL Freight Romania
- Elis Pavaje
- Green Group
- Mainfreight Romania
- OtelInox
- Toyota
DHL Freight Romania uses CargoTender to optimize its transport acquisition processes.
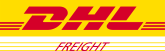
Within DHL Freight Romania we have decided to implement a transparent contract allocation procedure for the transport providers. That is why we searched for an easy way to automate this process. We chose CargoTender because it is a romanian freight tender platform, easy to use, efficient and provides a fair cost for its customers. It also ensures a transparent auction process.
Challenges
- The old classic auctions (closed covers) were not transparent and did not offer real-time data to our providers or the possibility to rephrase;
- A lot of time spent on data centralization and communication to suppliers;
Results
- Auctions have become much more transparent;
- Quick centralization of the results;
- Saving increased (3 - 5%);
About DHL Freight Romania
DHL Freight is a division of Deutsche Post DHL providing road and rail freight services across Europe, North Africa and the Middle East. Together with DHL Global Forwarding (formerly DHL Danzas), it forms Deutsche Post's Freight / Forwarding business division.
360,000 people are working now for DHL, in over 200 countries and they are delivering 1,394,000,000 parcels per year.
DHL Freight Romania provides a variety of logistics services tailored to customer's needs, from standardized logistics operations, multimodal transport solutions to individual industrial projects.
Elis Pavaje is using CargoPlanning for transparency and efficient freight allocations.
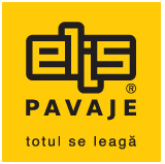
Time gained, transparency of decision - making process, cost reduction, efficient control of the activity, quick information for the employees, adaptability of the program to the customer's requirements and many other advantages made us to start collaborating with CargoPlanning at the end of 2017. Currently we have over 100 transport providers all over the country that are working with us on this platform, supporting us daily in carrying out the transport planning activity at Elis Pavaje Romania.
Challenges
- High volume of manual work (phone, email, excel) for planning over 100 daily shipments;
- Difficult communication with transport providers due to numerous channels;
- Long time dedicated to centralizing all reporting information;
Results
- Optimizing the procurement of transport services by 30%;
- Increased efficiency of the logistics team - all information is in one place, easy to access;
- Easily exchange of transport documents and communication with carriers;
About Elis Pavaje Romania
Elis Pavaje's story begins in 1991 as a small family business;
Today, Elis Pavaje is a team of of 500 employees;
Production of over 16,000 square meters / day;
4 production units: Stoenesti (Prahova) Petresti (Alba), Vintu de Jos (Alba), Secuieni (Neamt);
Annual turnover of 161.2 million lei in 2017
GreenTech & GreenFiber use CargoPlanning for transportation optimization and planning.
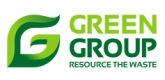
Green Group is the largest integrated waste recycling group in Central and Eastern Europe and a major player in the circular economy. With an installed recycling and production capacity of over 460,000 tons annually, Green Group makes an important contribution to the recovery of valuable materials from waste and to the acceleration of the circular economy in Europe. We would not have managed to reach these dimensions if we had not always been looking for new opportunities for development, transformation and innovation. We chose the partnership with the CargoPlanning platform to help us optimize the logistics processes within the group. The main reasons why CargoPlanning was the right choice are the team's innovation and capability. They demonstrated a good understanding of our needs and way of working and we achieved customized solutions. As a result of this collaboration, our logistics, sales and procurement teams have better internal communication and we have created a transparent and efficient process of collaboration with transport suppliers.
challenge
- Communication between the purchase/sales department and the logistics department;
- Centralization of orders from suppliers and customers;
- Real-time information regarding the status of an order;
- Transparency in collaboration with transport providers;
- Digitization of processes;
result
- Medium and long term transport planning;
- Increasing the efficiency of the logistics team;
- Faster and solution-oriented decision-making processes;
- Multiple options for solving transport orders;
GreenTech and GreenFiber have five subsidiaries and together have more than 13,000 customers and suppliers across Europe. Each of them was given access to the CargoOrder portal to enter their sales/purchase orders. The logistics team consolidates these orders into transport orders and they are allocated both through spot auctions organized in the CargoPlanning module and according to contracts established following tenders organized through the CargoTender module.
This worlflow facilitated the transmission of information both between departments and branches and towards customers and suppliers, while keeping a history of all orders. Planning shipments a month in advance, by organizing tenders, gives the whole team and management an assembly picture of the activity.
The reports obtained through the platform provide a solid basis for managing resources effectively and setting new goals. With an average of 1000 orders per month, all information is centralized in one place, including the digital documents submitted by the carriers.
GreenGroup is constantly looking for ways to improve processes, which has challenged us to improve our services. The next objective is to implement the CargoSlot module for planning and managing loading and unloading at warehouses. Platform modules are interconnected, which makes it possible to automatically transfer information between modules and simplifies the process of booking a slot.
ABOUT GREENTECH & GREENFIBER
GreenFiber and GreenTech are part of GreenGroup, which started their journey in 2002. Today, GreenGroup is an important embedded regional group of recycling and a promoter of the circular economy. GreenGroup is leader in the European market in the field of PET recycling and synthetic fiber production from recycled PET and a key player in the field of electronics recycling, glass waste recycling, and industrial waste recycling. Currently, the GreenGroup ecosystem comprises five major business divisions: PET packaging waste recycling, electrical and electronic waste (WEEE) recycling, glass packaging waste recycling, industrial waste management, and extended producer responsibility (EPR) for packaging waste
Mainfreight Romania chose CargoSlot for better control of warehouse operations.
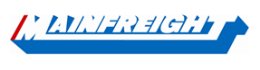
At Mainfreight Romania we want that our entire warehousing and domestic / international transport process be at a superior level of performance and efficiency, and with the speed and promptness offered, the customer will consider us the number one choice.
Why CargoPlanning?
The Mainfreight slogan is "Special People, Special Company", and that is why we need a personalized tool to meet the needs of our teams so that its use simplifies internal processes. The CargoPlanning platform has made a linear flow of means of transport, reduced waiting time, optimized the loading / unloading process, and created a linkage interface between departments within the company.
Challenges
- With the increase of activity the classic system used reached its limits of use so a specialized tool was needed;
- High waiting times for loading / unloading operations due to the uneven arrival of the means of transport;
- Difficult process of prioritizing operations;
- Lack of information about the position of the means of transport within the premises of Mainfreight warehouses;
Results
- Improved control over operations by switching from a limited system to a dedicated online booking slot system that, in addition to slots planning and modification, also ensures the visibility of the entire process through online access from any device connected to the Internet;
- Implement a status system that monitors the means of transport at different checkpoints inside the warehouse and records the time and date of passage (arrived at the gate, arrived at the ramp, left the ramp, finishing the operation);
- Reducing waiting times by scheduling slots and optimizing warehouse activity by organizing transport modes on time, resulting in maximizing operational capacity;
- Eliminate phone calls by automating the transmission of information by SMS or e-mail and by viewing statuses for each order by any CargoSlot user at any time of the day;
About Mainfreight Romania
Mainfreight offers storage services, road, sea and air transport and customs clearance;
200 work points across Europe, Australia, China, New Zealand and the United States;
4 locations in Romania: Ploiesti, Cluj - Napoca, Bacau and Buzau;
22,000 sqm of A class in Romania;
50 transport units;
250 employees in Romania;
OtelInox, part of Samsung C&T, uses CargoTender for freight procurement.
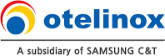
We started to work with the CargoPlanning platform since 3 years ago. We chose an online platform for freight tender thanks to the benefits offered - speed, transparency and automatic centralization of the results. We use to invite more than 40 transport providers and select the best offers for this kind of services. CargoTender was exactly what we needed at the right time. The main advantage was the time reduction for the entire process. The prices offered by the carriers were as expected and due to the introduction of the target price for each area.
Challenges
- Huge amount of data to handle with - we took a lot of phone calls and we used to exchange a lot of emails or to do paper work in order to find the best carriers for our shipments;
- Lack of transparency - we do care about our partners and we want to give everyone the same chances, so we wanted a collaborative system to provide real time data on the progress of the tender;
Results
- Streamlined the tendering process - the bidding time shortened from 2 weeks to 3 days;
- For 10% of the routes, we obtained lower prices than the proposed target price;
- Better control over the entire process - we focus on choosing the best offers instead of centralizing every information (the platform has a unique mechanism of centralizing the offers based on our needs);
About OtelInox Romania
Manufacturing company of special and laminated steels;
Founded on June 1, 1974;
Since 1997, Otelinox's majority stake ( GmbH;
60,000 tons per year - production capacity for stainless steel sheets and bands;
100,000 tons per year - production capacity for small profiles and wire
Toyota uses CargoPlanning for transparency and overview for the entire logistics department.
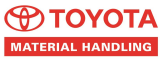
Our collaboration started in 2018, the tenacity of the sales representative having a special role. Today, would say without hesitation that we could not imagine our daily activity without the help of the platform. The logistics team has in TMHRO the role of a service provider: the main activity is the organization of the equipment movement, the needs (with different degrees of urgency) being expressed by different internal clients, dep. Sales, Rental, Service. Given that in a trivial delivery are most often involved about - 12 TMHRO employees, adding shipping company / carrier, customer, it is essential the flow of information to be fast and dynamic, synchronization of various stages and, finally, customer , can not be obtained otherwise. simplifies and supports this process both during the transport and after the delivery confirmation, when the administrative part must be executed any invoice must be paid, right?
challenge
- Many physical materials with daily printed shipping orders, which was inefficient for the logistics team;
- Communication mainly by email and telephone to inform the whole team about the status of an order, which is time consuming and did not provide real-time information;
- Difficulty following an order;
result
- Viewing all transport requests and the status of each of them more control over each operation, the need to various documents becoming minimal;
- Simplifying the process of allocating orders as well as sending them to suppliers two, three clicks) eliminates email or telephone , productivity being considerably improved;
- Quick and easy access to information all departments involved in the movement of equipment Logistics, Sales, Rental, Financial) ensures a well-organized work environment, the information thus structured facilitating communication;
- The ability to extract various reports is another important of the platform, many decisions and choices being made based a history always at hand.
ABOUT TOYOTA
Toyota Material Handling Romania is part of the Toyota Material Handling Europe group, integrated in turn into Toyota Industries Corporation, the world leader in the field of production of equipment for . The experience of over 5 years of group, the resources allocated to research and development, as well as the know-how in field, is materialized in high quality equipment, which incorporates a top technology, produced with TPS (Toyota Production Sysem).